Sementert karbid er et pulvermetallurgiprodukt sintret i en vakuumovn eller en hydrogenreduksjonsovn med kobolt, nikkel og molybden som den viktigste komponenten i tungsten-karbidmikronstørrelse av pulver av høy hardere metall. Sintring er et veldig kritisk trinn i sementert karbid. Den såkalte sintringen er å varme opp pulverkompakt til en viss temperatur, holde det i en viss periode og deretter avkjøle det for å få et materiale med de nødvendige egenskapene. Sintringsprosessen med sementert karbid er veldig komplisert, og det er lett å produsere sintret avfall hvis du ikke er forsiktig. I dag vil Chuangrui Xiaobian dele med deg det vanlige sintret avfall og årsakene.
1.
Det vil si at overflaten på det sementerte karbidet passerer gjennom sprekker på kantene, skjevt skjell eller sprekker, og i alvorlige tilfeller, små tynne skinn som fiskeskala, sprekker og til og med pulverisering. Skallingen skyldes hovedsakelig kontakteffekten av kobolt i kompakten, slik at den karbonholdige gassen dekomponerer fritt karbon i den, noe som resulterer i en reduksjon i den lokale styrken til kompakten, noe som resulterer i peeling.
2. det nest vanligste sementerte karbidsinterte avfallet er hull
Porer over 40 mikron kalles porer. Faktorer som kan forårsake blemmer kan danne porer. I tillegg, når det er urenheter i den sintrete kroppen som ikke er fuktet av det smeltede metallet, for eksempel store porer som "upresset", eller den sintede kroppen har alvorlig fast fase og segregeringen av væskefasen kan danne porer.
3. det tredje vanligste sementerte karbidsinters avfallsproduktet er blemmer
Det er hull i de sementerte karbidlegeringsproduktene, og konvekse buede overflater vises på overflaten av de tilsvarende delene. Dette fenomenet kalles blemmer. Hovedårsaken til blemmer er at den sintrete kroppen har relativt konsentrert gass. Det er vanligvis to slag: den ene er at luften samler seg i den sintrete kroppen, og under den sintringsryssprosessen beveger luften seg fra innsiden til overflaten. Hvis det er urenheter av en viss størrelse i den sintrete kroppen, for eksempel legeringsrester, jernrester og koboltrester, vil luften konsentrere seg her. Etter at den sintrete kroppen dukker opp i en flytende fase og er fortett, kan ikke luften slippes ut. Blemmer dannes på de minste overflatene.
Det andre er at det er en kjemisk reaksjon som genererer en stor mengde gass i den sintrete kroppen. Når det er noen oksider i den sintrete kroppen, reduseres de etter at væskefasen ser ut til å generere gass, noe som vil gjøre produktet boble; WC-Co-legeringer er vanligvis sammensatt av forårsaket av agglomerering av oksider i blandingen.
4. Det er også ujevn organisasjon: miksing
5, og så er det deformasjon
Den uregelmessige formendringen av den sintrete kroppen kalles deformasjon. De viktigste årsakene til deformasjonen er som følger: tetthetsfordelingen av kompaktene er ikke ensartet, fordi tettheten til den ferdige legeringen er den samme; Den sintrete kroppen mangler alvorlig karbon lokalt, fordi mangelen på karbon reduserer væskefasen relativt; Båtbelastningen er urimelig; Støtteskaten er ujevn.
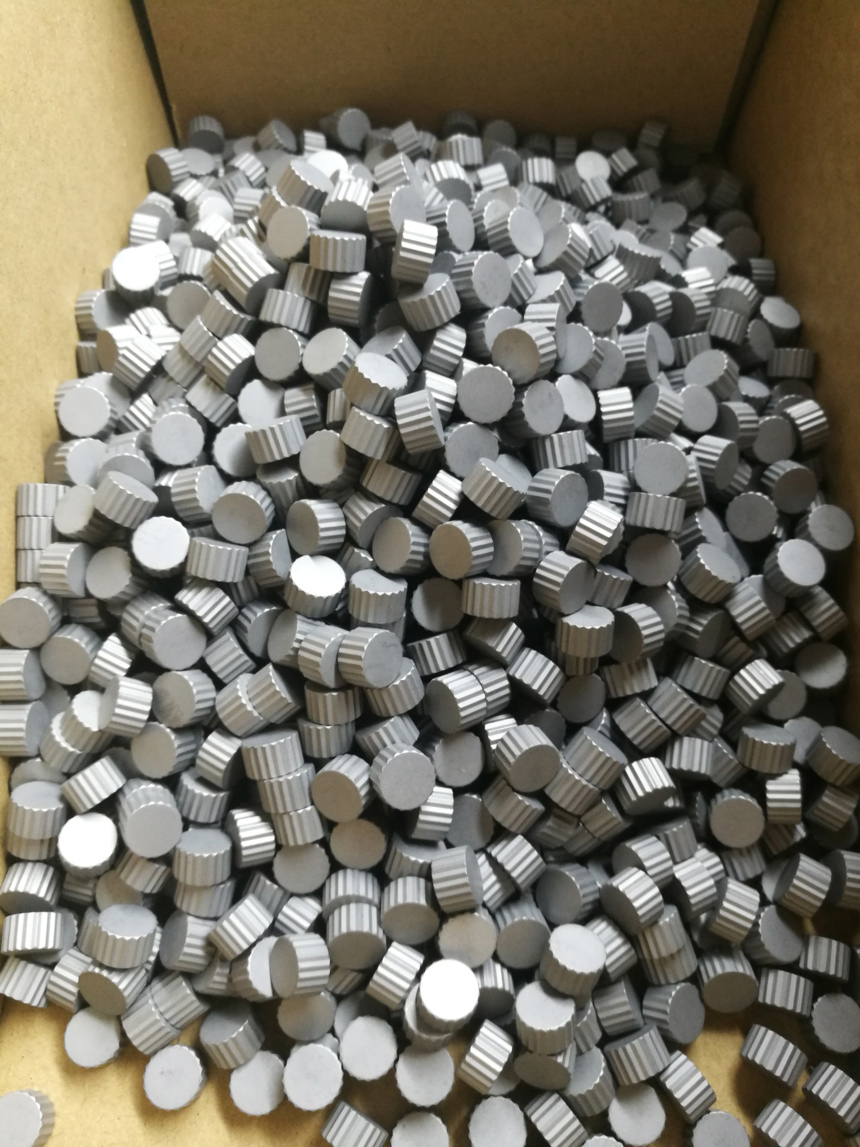
6. Svart hjerte
Det løse området på legeringsbruddoverflaten kalles Black Center. Hovedårsaker: For lite karboninnhold og upassende høyt karboninnhold. Alle faktorer som påvirker karboninnholdet i det sintrete kroppen vil påvirke dannelsen av svarte hjerter.
7. Sprekker er også et vanlig fenomen i sementerte karbidsinterte avfallsprodukter
Kompresjonssprekker: Fordi trykkavslappingen ikke viser seg umiddelbart når briketten er tørket, er den elastiske utvinningen raskere under sintring. Oksidasjonsspriser: Fordi briketten er delvis oksidert når den er tørr, er den termiske ekspansjonen av den oksiderte delen forskjellig fra den for den ikke -oksiderte delen.
8. Overbrenning
Når sintringstemperaturen er for høy eller holdetiden er for lang, vil produktet bli overbrent. Overforbrenningen av produktet gjør kornene tykkere, porene øker, og legeringsegenskapene avtar betydelig. Den metalliske glansen av underfyrte produkter er ikke åpenbar, og den trenger bare å bli avfyrt på nytt.
Post Time: Mai-31-2023